Although organic farming only accounts for less than 1% of total U.S. farmland, it’s a niche that continues to grow. In fact, USDA research shows that U.S. certified organic cropland grew 40% from 2016 to 2021, expanding from a little over 2.5 million acres to a little over 3.5 million. That growth is taking place all over the country, too, even in the Corn Belt.
With so much attention given to fruits and vegetables, organic row-crop farming can be an overlooked segment of the market. But it’s a segment farm equipment dealers shouldn’t ignore. Organic row-crop growers have as much of a need for equipment as conventional growers — perhaps even more so.
While they may not need chemical sprayers, organic growers still need tractors, planters and harvesting equipment. They also need a variety of tillage implements, along with several unique pieces of weed control equipment.
“Organic farmers tend to stick together. As a dealer, word of mouth is huge…”
“If a farmer does a really good job with weed control, especially early in the year, while also staying in touch with the agronomic side of their ground, yield really shouldn’t change much when farming organically,” says Mark Jacoby, owner of Great Lakes AG Equipment in Akron, Mich., a dealership that sells equipment geared toward weed control in organic farming, including Einböck cultivators and tine weeders.
Jacoby is also a fourth-generation farmer, though he only transitioned to organics 5 years ago. He became a dealer shortly thereafter in 2020. Today, in addition to running his dealership, Jacoby organically farms around 1,200 acres of dry beans, soybeans and corn.
“We’re producing the same amount we produced when farming conventionally,” Jacoby says.
Establishing Trust
To sell equipment to an organic production farmer, dealers need to build trust. That starts with showing a genuine appreciation for what an organic grower is trying to accomplish.
Takeaways
- Express a genuine interest in what organic growers are trying to do, which will help spark connections among a tight-knit segment of the farming community.
- Ask a lot of questions to help determine what the customer’s biggest challenges and objectives are, which will help determine the right cultivation, planting and harvesting solutions for their needs.
- Consider stocking specialized equipment that meets the unique needs of organic growers, such as tine weeders, propane flamers and electric weed
“An organic farmer is kind of like the black sheep in the farming community in a lot of places,” says Ron Fleming, sales manager and equipment specialist at Crop Fertility Services (CFS) in Cokato, Minn. “Because of that, organic farmers tend to stick together. As a dealer, word of mouth is huge.”
Generating word of mouth came somewhat naturally to CFS, which consists of a group of organic farmers who got together to sell organic-based fertilizers in 2012. CFS gradually added staff and branched into equipment sales in 2019. CFS is now a multi-state dealer for Hatzenbichler and Salford cultivators, along with Hatzenbichler tine weeders and finger weeders. CFS also custom-builds propane weed burners they call Row Crop Flamers. They even put on a popular event every August called The Organic Farm Innovation Expo.
Speaking of innovation, that’s another way dealers can make a connection with the organic farming community.
“One of the biggest differences between conventional and organic growers is mentality,” says Jonathan Hostetler, owner of TH Fabrication in El Paso, Ill., a manufacturer of cultivators designed specifically for organic growers. “I hate to paint with too wide a brush, but conventional farming is a little more reactive. Organic farming is more proactive. Getting at a weed before it gets big can make all the difference. Anything a manufacturer and dealer can do to provide options that help save time and stay ahead of problems is really appreciated by organic farmers.”
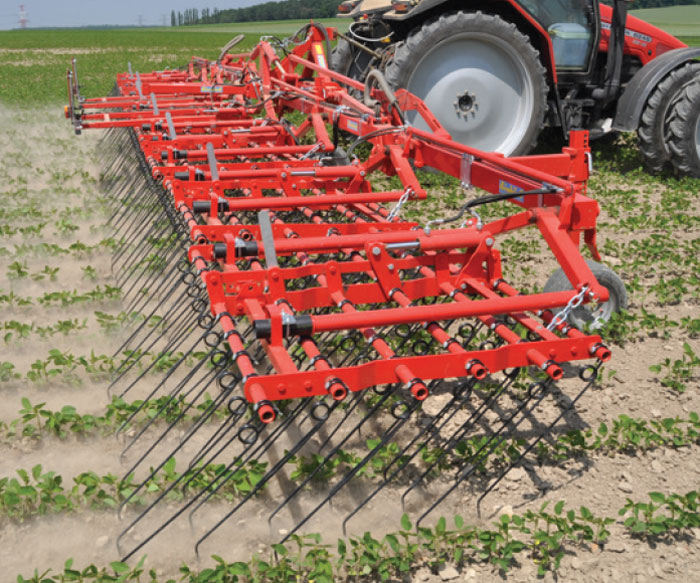
Einböck’s Aerostar Tine Weeder incorporates movable tine sections to help the implement adapt to varying soil conditions. Additionally, the vibration of the spring-loaded tines helps ensure the tines won’t clog while uprooting weeds from the soil. Photo by: FarmPower Distribution
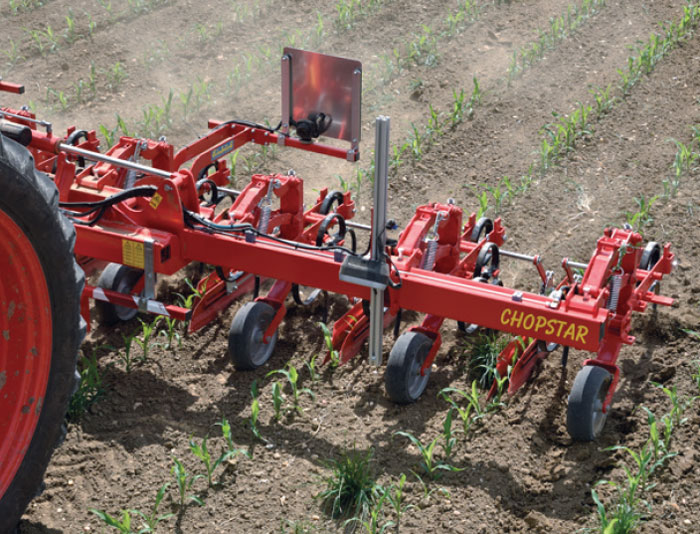
Einböck’s Chopstar Cultivator is designed to not only control weeds, but also improve soil aeration, nitrogen mobilization and regulation of water balance. For added versatility, weeder tines can be mounted on the hoeing sections. Finger weeders are another popular add-on. Photo by: FarmPower Distribution
“A dealer has to be open-minded to our way of farming and must be receptive to finding unconventional ways of solving our problems,” adds Alex Hopkins, owner of Hopkins Agriculture in Malta, Ill., a dealer for Buffalo cultivators since 2020.
Hopkins has also been helping his father-in-law organically farm more than 4,000 acres of row crops, a corn/soybean/oat rotation. “The organic growers in our area, ourselves included, are looking to buy equipment that is innovative in controlling weeds, while also helping us be better stewards of the land. Both are very important.”
Routine Equipment for Specialized Needs
Conventional and organic production farmers have several overlapping equipment needs. However, how and when organic growers use certain equipment may be a bit different. This is where a dealer can ask questions to help match tool to task, and time of season.
“Good weed control starts before planting, using a tillage implement that effectively removes weeds…” – NAME
“I like to find out how long they’ve been farming organically,” Jacoby says. “I like to find out which pieces of equipment they’ve been using thus far, especially when it comes to weed control. I also like to find out what kind of weed issues they’ve been having. Are their biggest struggles with early season weeds, or maybe later in the season? Once I get some answers, I walk backward to start matching the right equipment solutions to whatever that customer’s specific needs are.”
As Hopkins points out, an organic farmer often wants several tools in their weed-combating toolbox. Common equipment used on a regular basis includes rotary hoes, field cultivators and row cultivators.
“Good weed control starts before planting, using a tillage implement that effectively removes weeds while also leaving the ground loose to mitigate seed-to-soil contact for weeds,” Hopkins says. For that reason, Hopkins stays away from discs and rollers. Rather, he likes field cultivators that work down 4 or 5 inches, but still leave the seedbed loose and fluffy.
Jacoby also likes to start the season with a field cultivator as soon as conditions allow. It’s not uncommon for him to hit a field three times before planting.
A rotary hoe will often come into play shortly after planting, before eventually giving way to a field cultivator.
“A rotary hoe is a good choice for pre-emerge and immediate post-emerge,” Fleming says. “When the crop gets a little bigger, you start needing a cultivator. When the crops gets even bigger, you may want a different cultivator because the last one threw too much dirt. With mechanical weed control, timing is half the battle. It’s really important to use the right tool at the right time.”
That’s why organic farmers are receptive to innovation and the thought of packing as many tools in the toolbox as possible. That said, most don’t have endless resources, which is why organic farmers are also eager to hear about equipment that’s versatile.
Take cultivators, for instance. Hopkins says it’s helpful for dealers to highlight features that enable a machine to not only cultivate small weeds early in the year, but also work later in the season when crops, weeds and field conditions are more intense.
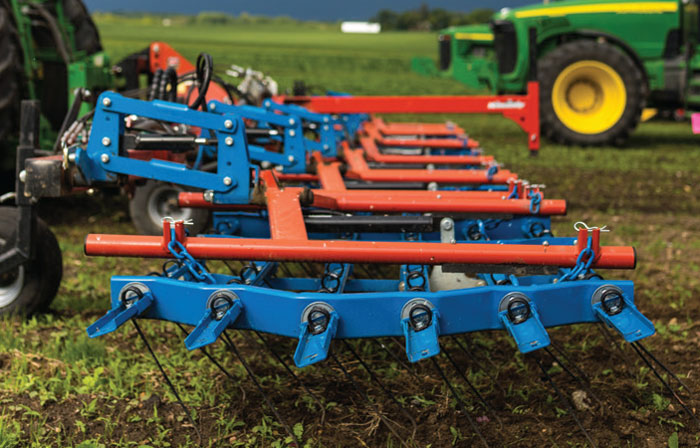
Hatzenbichler’s Tine Weeder has a unique design that exerts down-pressure on each individual tine section. That helps ensure thorough and consistent weeding throughout a field, regardless of hills and dips. These tine weeders have also been carefully designed to incorporate slightly fewer tines that are spaced slightly farther apart. This helps improve trash flow while still optimizing soil disturbance and weeding action. Photo by: Crop Fertility Services
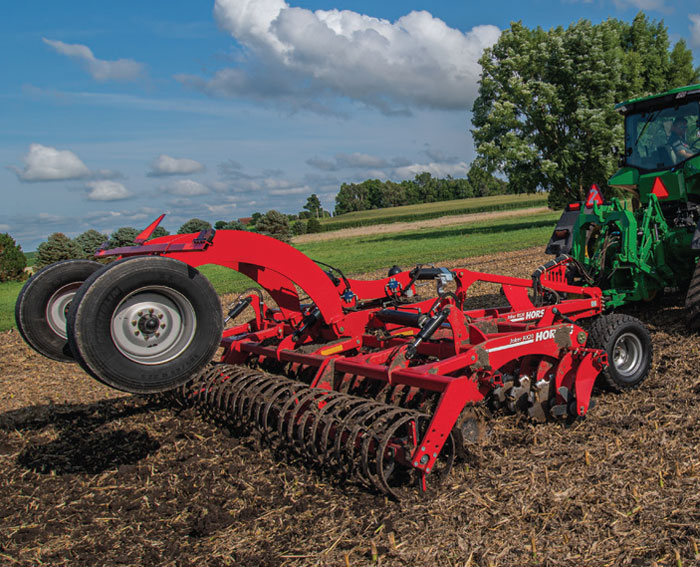
Horsch's Joker RX disc harrow has become popular among organic growers, says Jeremy Hughes, marketing product manager at Horsch. The 17/17 front/rear blade engagement angle helps size and mix residue and ensures a thorough horizontal fracture for enhanced weed kill prior to planting. Photo by: Horsch
A key area of innovation is the camera guidance system, which attaches to a cultivator to make it considerably more precise and productive. Jacoby says some of his customers will buy a new cultivator with a camera system, and sometimes they just buy a camera system to mount on a cultivator they already own. In either case, Jacoby is happy to help — because camera guidance is a solution that can help an organic grower achieve their ultimate goal.
“If you can get closer to the row and do a really good job with early weed control, it’s going to make all the difference,” Jacoby says. “If the price of soybeans is $20 a bushel, and you can gain 5 bushels per acre, that’s $100 an acre. If you’re farming 500 or more acres, that camera guidance system is going to easily pay for itself in one year.”
As important as mechanized weed control is, organic farmers do more than just till soil. When it comes to planting equipment, Jacoby says the needs are quite similar to a conventional grower. “One difference is an organic farmer might be doing more in-furrow organic liquid fertilizer application, so they may be looking for some different types of attachments,” Jacoby points out.
There may also be some unique preferences with harvesting equipment. Hopkins says an organic farmer may want to stress quality over quantity. So when spec’ing a new combine, they may prefer a general-purpose concave over a deep-tooth sieve. That’s another conversation the dealer will want to have to help match the right solution to that customer’s needs.
Specialized Equipment for Routine Needs
Another common tool in an organic grower’s toolbox is a tine weeder. While it’s more specialized than a cultivator or rotary hoe, it is still routinely needed. In fact, for early season and in-season weed control, Jacoby says a tine weeder is the most essential piece of equipment an organic operation can have.
“Science has proven that weed seeds are already germinating within 4 hours of planting,” Jacoby says. On his farm, Jacoby uses a tine weeder within 24 hours of planting, making what he calls the “blind tine weed pass” to take out weed seeds in the top 0.5-0.75 inches of soil. He’ll often follow that with a second round 2 or 3 days later. Jacoby also likes to tine weed after the crop has emerged. That’s because a tine weeder is tough on weeds, yet delicate enough to work in sensitive crops.
“You can use a tine weeder when soybeans are at their two-leaf stage,” Jacoby points out. “You can hit corn when it’s about 1.5 inches tall. You have to go slow, but you can use it.”
Not all tine weeders are created equal, though. Again, it’s important for a dealer to ask questions to help match the right solution to that customer’s specific needs. For instance, the type of ground may influence the length and thickness of the tine that’s best. Additionally, some tine weeders feature hydraulic tine pressure adjustment to enhance performance in changing soil conditions.
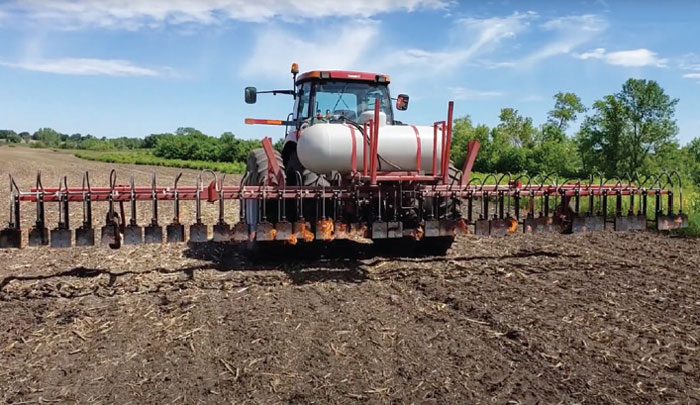
Kadelbach’s Propane Flame Weeders are unique in that each burner has two orifices. If one flames goes out, the second flame immediately reignites it. This helps prevent flameout in the field which negatively impacts coverage, productivity and ROI. Kadelbach Flame Weeders go all the way up to 24-row for high-acreage organic row-crop farmers. Pictured here is a 12-row, the Model 12R30. Photo by: Kadelbach Mfg.
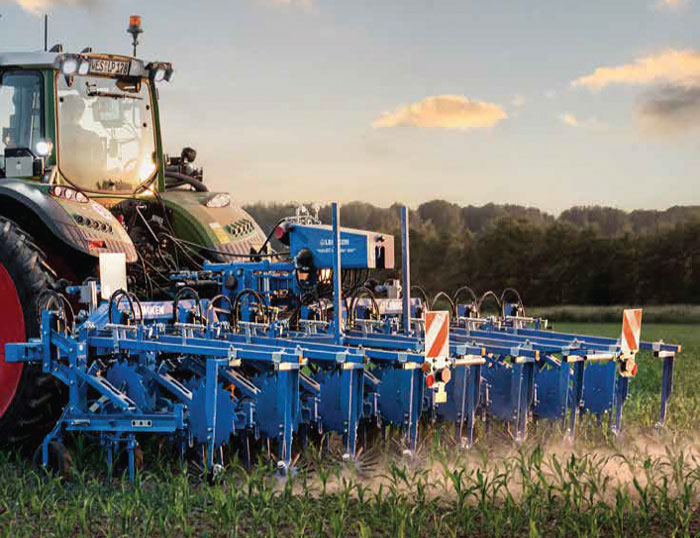
Lemken’s EC-Weeder is a fully customizable hoeing machine that allows users to make adjustments to adapt to changing soil conditions, growth stages and row spacing. Numerous tool options are also available including tines, crumble rotors, rotor weeders and finger weeders. Photo by: Lemken
Other tine weeders feature unique design elements that help ensure consistent coverage across uneven fields. Again, timing is everything with mechanical weed control. It’s helpful to call attention to unique features that help improve the versatility, consistency and reliability of a tine weeder.
One more specialized weed-control solution is a finger weeder, which attaches to a cultivator. A finger weeder can provide an advantage during cultivating because it can get really close to the crop. It’s one of those tools that might not be used all the time but is certainly handy to have in the toolbox for when it’s needed.
Solutions for ‘Rescue’ Situations
A well-timed regimen of cultivating and weeding can be all it takes for an organic grower to stay ahead of weeds. But precise timing requires Mother Nature to always cooperate. What are the odds of that happening? That’s why an organic grower may want to add a couple more tools to their toolbox.
Propane flame weeders and high-voltage electric weeders can prove useful when ground conditions aren’t conducive to cultivation, such as when it’s really wet. These tools can also help deal with weeds that have escaped previous weed control methods.
“When an organic grower is talking about weeds, there’s often a bit of desperation in their voice,” says Ben Kroeger, co-owner of Old School Mfg. in Sedalia, Mo., maker of The Weed Zapper. “You can never quite win the battle. That’s where a product like The Weed Zapper comes in.”
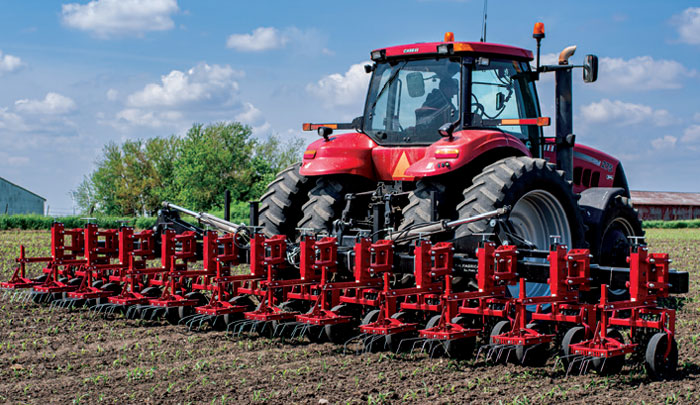
TH Fabrication’s Rotary Hoe Pro adds gauge wheels to a standard rotary hoe so operators can hold a consistent depth. Additionally, gangs are run at an angle to better agitate the dirt. Attachments can also be added to the rear of the implement to increase versatility and productivity. Pictured here is a tine weeder attached to the rear of the machine. Photo by: TH Fabrication
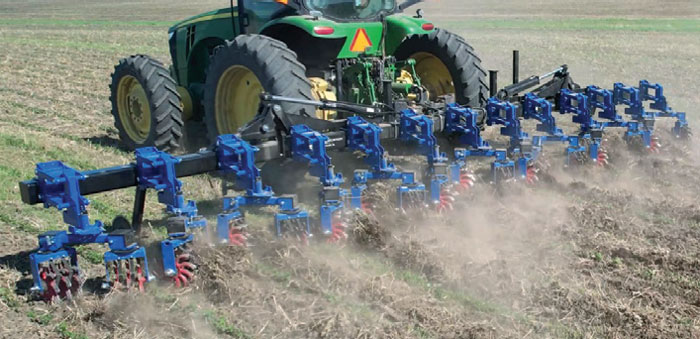
TH Fabrication’s Swinging Spider has taken the classic Lilliston rolling cultivator and added a patented feature that makes it easy to adjust each gang of spider wheels in the field without tools. Users just need to grab the handle and swing the arm, allowing for quick configurations to get closer to the row, and either throw dirt away from or onto the row. Optional finger weeder attachments can also be added for simultaneous in-row weed control. Photo by: TH Fabrication
The Weed Zapper is a unique piece of equipment that uses 100,000-plus watts of electricity to kill weeds. Pat Kruger, owner of Farmn Inc. in Montevideo, Minn., became a dealer in 2021 after having used a Weed Zapper for several years as an organic sugar beet farmer. Between his own acreage and the fields he custom-zaps for other growers, Kruger uses a Weed Zapper on roughly 5,000 acres per year.
Kruger uses Weed Zapper’s tractor-mounted solution called the Annihilator. For his organic row-crop customers, the 16R30 is the most popular size. “It’s a 40-foot bar that mounts to a tractor, and most row-crop farmers like it because it’s the biggest of the cheapest,” Kruger says.
By “cheapest” Kruger means less expensive than Weed Zapper’s Terminator model, which is a dedicated machine that’s three times the price. Still, some high-acreage organic row croppers see a dedicated machine as a better investment because it eliminates the need to tie up one of their tractors with an attachment.
“The Terminator can also go through taller fields because it’s on a sprayer chassis,” Kruger points out. “The tractor-drawn Annihilator, on the other hand, is only 18-22 inches off the ground. That can push those late-season beans pretty hard.”
Regardless of which style of Weed Zapper he sells, Kruger says safety is a customer’s biggest concern. To help ease the customer’s mind, he always spends considerable time going over the numerous built-in safety features on the machine. He also explains the handful of “operator errors” that can compromise safety. “The main thing is to avoid coming into contact with the machine when it’s live,” Kruger says. “Never approach the machine when someone else is operating it. Other than that, you’re safe.”
When a customer purchases a Weed Zapper, Kruger emails them the manufacturer’s essential safety documentation as reinforcement, as well as links to training videos. He also makes himself available to answer any questions. Sometimes those questions have nothing to do with safety.
“The first week after someone buys their first Weed Zapper, my phone is blowing up because the weeds aren’t dying like they should,” Kruger relates. That’s because first-time operators often don’t recognize the importance of going slow and steady. There are also voltage settings that can be adjusted for different types of weeds and moisture conditions.
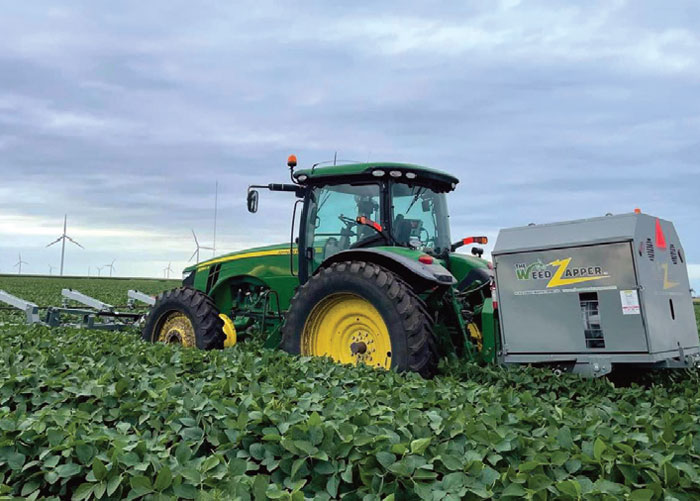
The Weed Zapper Annihilator is a tractor-mounted weed-control solution that uses 100,000-plus watts of electricity to kill weeds. It consists of a cart/generator that attaches to the 3-point-hitch at the rear of the tractor. A boom is then attached to the front of the tractor where the voltage comes out. Photo by: Old School mfg.
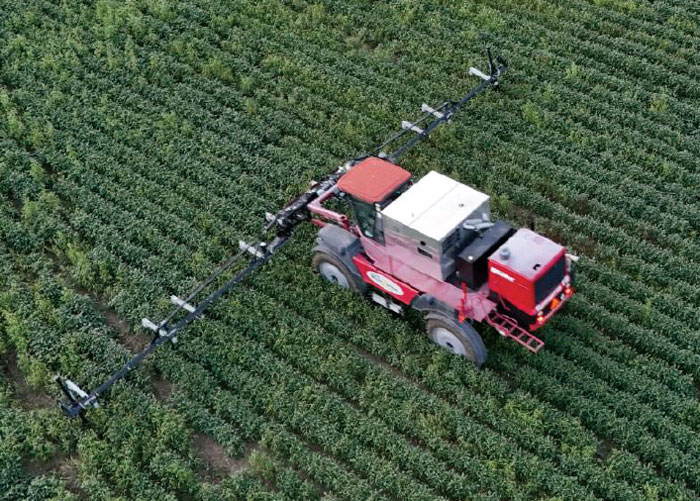
The Weed Zapper Terminator is a dedicated weed-control solution that uses 100,000-plus watts of electricity to kill weeds. It’s a feasible solution for large-acreage row crop growers who don’t want to tie up a tractor with an attachment for several months each season. Photo by: Old School mfg.
“For example, if it’s really dry, you may need to increase the voltage to break the resistance in the ground and make sure the weeds are killed,” Kruger says. He goes over all of that with the customer and makes himself available to answer any questions as they’re navigating their learning curve.
Propane flame weeders also require a bit of a learning curve. And like with electric weeders, new users often have questions regarding safety.
“Our flamers are designed with built-in safety mechanisms, too, like shutoff valves on the two outside burners,” says Glen Kadelbach, owner of Kadelbach Mfg. in Hutchinson, Minn., a manufacturer of propane flame weeders.
“We also recommend that an operator carry a 2- or 3-gallon sprayer full of water as an added safety measure. But once a farmer gets accustomed to flame weeding, it’s really no different than cultivating.”
Whereas electric weeders are an effective solution when weeds are taller than the crop, propane flamers are ideal when weeds are closer to the ground, perhaps up to 5 inches tall. “Flame weeders are also effective at cleaning up in the row, especially under taller crops like corn,” says Kadelbach, who has been a certified organic farmer since 2011.
“On the other hand, soybeans are a riskier application because some pods could be touching the ground and get damaged by the flame. That’s why I use both a flamer and an electric weeder in my own organic operation. Each has its place, and both are needed.”
There is one other rescue-type tool that Jacoby sells called the Meneguzzo weed trimmer. He says this less expensive, tractor-mounted solution can come in handy later in the season to cut back rogue weeds before they go to seed. “Some customers also like to use it in soybeans right before podding,” he says. “They like to top off that top inch while cutting weeds at the same time.”
Fleming, Hopkins and Jacoby all agree that “rescue” tools may never be needed if the farmer is doing a good, proactive job with their rotary hoes, cultivators and tine weeders. But you just never know when Mother Nature or other variables may get in the way of doing a good job.
Since timing is everything in organic row cropping, there’s always going to be a time when an organic farmer is happy to have as many tools to fall back on as possible.