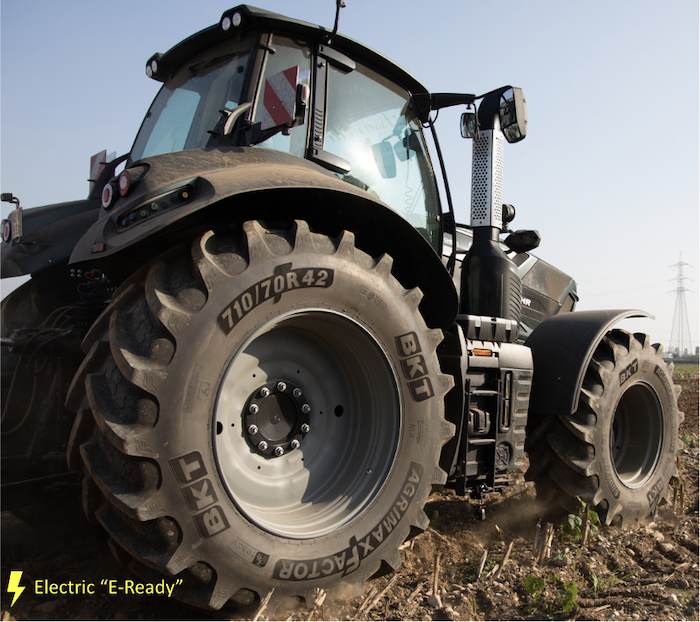
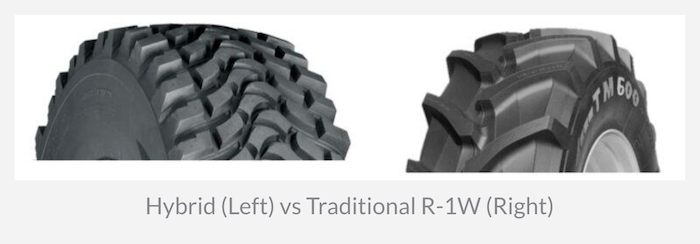
- Compact and support tractors below 50 HP represent the greatest immediate opportunity for electric engines and market sustainability solutions. Most of these lower HP engines are primarily used in smaller farming operations, where compaction due to heavier wheelbase weight is less of an issue due to their role as support machinery with limited weight towing requirements. These types of lighter ag applications are less demanding as higher horsepower tractor platform market demands and therefore represent an easier platform to develop short-range or limited battery life offerings capable of evolving into higher HP applications.
- The +50 HP up to 130 HP power range will be the true test of electric developments as these represent the largest global segment of tractors in the market. As tractors above +50 HP are used as production machinery in smaller farms less than 400 acres, dairy operations, or ranching applications, the longevity of battery life and recharging capability to deliver the utility time or productivity required to do the job will be tested. Although increased soil compaction can become a problem in farming use due to the wheelbases potentially becoming heavier, the use of VF tire technology can help offset some of the ground pressure or load requirements to reduce the pressure impact.
- The +125 HP platforms and up to +600 HP 4WD Tractors will be the frontier of alternative fuels or energy as their mission is centered on heavy-duty farming with large fields of more than 400 acres requiring autonomy, fuel range, and power transmission to tow the heaviest pieces of support equipment. The most significant challenge to this equipment is battery life and rechargeability in a remote field application. In the short term, alternative fuels such as methane are delivering realistic and sustainable fuel solutions that consume liquid manure as a source of energy. The CNHI New Holland brand of machinery has already released two platforms in their T6 (+125 to 175 HP) and T7 (+150HP to 300 HP) tractor product offerings that is using methane as the fuel source to power their engines via the consumption of biodegradable animal waste. If battery technology improvements can be achieved, then electrification can deliver the power needed for these larger tractors.
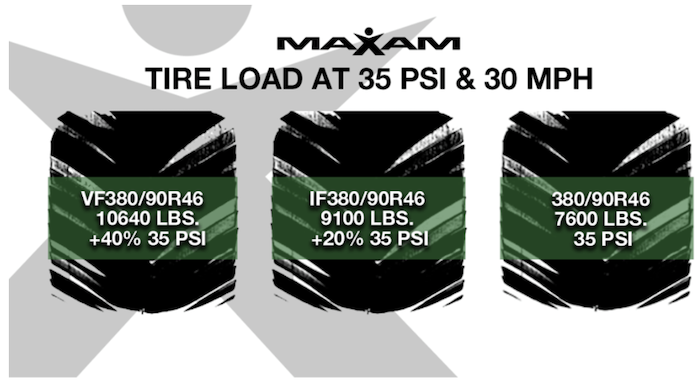